- Blog Categories
- Project Management
- Agile Management
- IT Service Management
- Cloud Computing
- Business Management
- Business Intelligence
- Quality Engineer
- Cyber Security
- Career
- Big Data
- Programming
- Most Popular Blogs
- PMP Exam Schedule for 2024: Check PMP Exam Date
- Top 60+ PMP Exam Questions and Answers for 2024
- PMP Cheat Sheet and PMP Formulas To Use in 2024
- What is PMP Process? A Complete List of 49 Processes of PMP
- Top 15+ Project Management Case Studies with Examples 2024
- Top Picks by Authors
- Top 170 Project Management Research Topics
- What is Effective Communication: Definition
- How to Create a Project Plan in Excel in 2024?
- PMP Certification Exam Eligibility in 2024 [A Complete Checklist]
- PMP Certification Fees - All Aspects of PMP Certification Fee
- Most Popular Blogs
- CSM vs PSM: Which Certification to Choose in 2024?
- How Much Does Scrum Master Certification Cost in 2024?
- CSPO vs PSPO Certification: What to Choose in 2024?
- 8 Best Scrum Master Certifications to Pursue in 2024
- Safe Agilist Exam: A Complete Study Guide 2024
- Top Picks by Authors
- SAFe vs Agile: Difference Between Scaled Agile and Agile
- Top 21 Scrum Best Practices for Efficient Agile Workflow
- 30 User Story Examples and Templates to Use in 2024
- State of Agile: Things You Need to Know
- Top 24 Career Benefits of a Certifed Scrum Master
- Most Popular Blogs
- ITIL Certification Cost in 2024 [Exam Fee & Other Expenses]
- Top 17 Required Skills for System Administrator in 2024
- How Effective Is Itil Certification for a Job Switch?
- IT Service Management (ITSM) Role and Responsibilities
- Top 25 Service Based Companies in India in 2024
- Top Picks by Authors
- What is Escalation Matrix & How Does It Work? [Types, Process]
- ITIL Service Operation: Phases, Functions, Best Practices
- 10 Best Facility Management Software in 2024
- What is Service Request Management in ITIL? Example, Steps, Tips
- An Introduction To ITIL® Exam
- Most Popular Blogs
- A Complete AWS Cheat Sheet: Important Topics Covered
- Top AWS Solution Architect Projects in 2024
- 15 Best Azure Certifications 2024: Which one to Choose?
- Top 22 Cloud Computing Project Ideas in 2024 [Source Code]
- How to Become an Azure Data Engineer? 2024 Roadmap
- Top Picks by Authors
- Top 40 IoT Project Ideas and Topics in 2024 [Source Code]
- The Future of AWS: Top Trends & Predictions in 2024
- AWS Solutions Architect vs AWS Developer [Key Differences]
- Top 20 Azure Data Engineering Projects in 2024 [Source Code]
- 25 Best Cloud Computing Tools in 2024
- Most Popular Blogs
- Company Analysis Report: Examples, Templates, Components
- 400 Trending Business Management Research Topics
- Business Analysis Body of Knowledge (BABOK): Guide
- ECBA Certification: Is it Worth it?
- How to Become Business Analyst in 2024? Step-by-Step
- Top Picks by Authors
- Top 20 Business Analytics Project in 2024 [With Source Code]
- ECBA Certification Cost Across Countries
- Top 9 Free Business Requirements Document (BRD) Templates
- Business Analyst Job Description in 2024 [Key Responsibility]
- Business Analysis Framework: Elements, Process, Techniques
- Most Popular Blogs
- Best Career options after BA [2024]
- Top Career Options after BCom to Know in 2024
- Top 10 Power Bi Books of 2024 [Beginners to Experienced]
- Power BI Skills in Demand: How to Stand Out in the Job Market
- Top 15 Power BI Project Ideas
- Top Picks by Authors
- 10 Limitations of Power BI: You Must Know in 2024
- Top 45 Career Options After BBA in 2024 [With Salary]
- Top Power BI Dashboard Templates of 2024
- What is Power BI Used For - Practical Applications Of Power BI
- SSRS Vs Power BI - What are the Key Differences?
- Most Popular Blogs
- Data Collection Plan For Six Sigma: How to Create One?
- Quality Engineer Resume for 2024 [Examples + Tips]
- 20 Best Quality Management Certifications That Pay Well in 2024
- Six Sigma in Operations Management [A Brief Introduction]
- Top Picks by Authors
- Six Sigma Green Belt vs PMP: What's the Difference
- Quality Management: Definition, Importance, Components
- Adding Green Belt Certifications to Your Resume
- Six Sigma Green Belt in Healthcare: Concepts, Benefits and Examples
- Most Popular Blogs
- Latest CISSP Exam Dumps of 2024 [Free CISSP Dumps]
- CISSP vs Security+ Certifications: Which is Best in 2024?
- Best CISSP Study Guides for 2024 + CISSP Study Plan
- How to Become an Ethical Hacker in 2024?
- Top Picks by Authors
- CISSP vs Master's Degree: Which One to Choose in 2024?
- CISSP Endorsement Process: Requirements & Example
- OSCP vs CISSP | Top Cybersecurity Certifications
- How to Pass the CISSP Exam on Your 1st Attempt in 2024?
- Most Popular Blogs
- Best Career options after BA [2024]
- Top Picks by Authors
- Top Career Options & Courses After 12th Commerce in 2024
- Recommended Blogs
- 30 Best Answers for Your 'Reason for Job Change' in 2024
- Recommended Blogs
- Time Management Skills: How it Affects your Career
- Most Popular Blogs
- Top 28 Big Data Companies to Know in 2024
- Top Picks by Authors
- Top Big Data Tools You Need to Know in 2024
- Most Popular Blogs
- Web Development Using PHP And MySQL
- Top Picks by Authors
- Top 30 Software Engineering Projects in 2024 [Source Code]
- More
- Tutorials
- Practise Tests
- Interview Questions
- Free Courses
- Agile & PMP Practice Tests
- Agile Testing
- Agile Scrum Practice Exam
- CAPM Practice Test
- PRINCE2 Foundation Exam
- PMP Practice Exam
- Cloud Related Practice Test
- Azure Infrastructure Solutions
- AWS Solutions Architect
- AWS Developer Associate
- IT Related Pratice Test
- ITIL Practice Test
- Devops Practice Test
- TOGAF® Practice Test
- Other Practice Test
- Oracle Primavera P6 V8
- MS Project Practice Test
- Project Management & Agile
- Project Management Interview Questions
- Release Train Engineer Interview Questions
- Agile Coach Interview Questions
- Scrum Interview Questions
- IT Project Manager Interview Questions
- Cloud & Data
- Azure Databricks Interview Questions
- AWS architect Interview Questions
- Cloud Computing Interview Questions
- AWS Interview Questions
- Kubernetes Interview Questions
- Web Development
- CSS3 Free Course with Certificates
- Basics of Spring Core and MVC
- Javascript Free Course with Certificate
- React Free Course with Certificate
- Node JS Free Certification Course
- Data Science
- Python Machine Learning Course
- Python for Data Science Free Course
- NLP Free Course with Certificate
- Data Analysis Using SQL
Six Sigma in Operations Management [A Brief Introduction]
Updated on Oct 28, 2022 | 14 min read | 18.1k views
Share:
Table of Contents
- What is Six Sigma in Operations Management?
- Six Sigma Principles for Operations Improvement
- Importance of Six Sigma in Operations Management
- Six Sigma Approaches for Operations Management
- Six Sigma Tools for Operations Management
- Implementing Six Sigma Initiatives in Ops Management
- Real-life Use cases of Six Sigma in Ops Management
- Benefits of Six Sigma for Operations Management Professionals
- Is Six Sigma Right for Your Company?
- Conclusion
The Six sigma methodology is a quality improvement approach used in operations management. It seeks to find and eliminate defects in manufacturing and business processes. The Six sigma approach in operations management is data-driven and relies on statistical methods to identify and correct process defects. Six Sigma aims to reduce process variation and improve process quality.
In this article, you will gain in-depth knowledge about how Six sigma impacts operations in the production and service industry. In addition, you will gain knowledge about the tools and principles of Six Sigma in operations management along with the benefits of Six Sigma in operations management. You can choose from various courses on Six Sigma if you wish to know more about this exciting methodology. These courses focus on the importance of the Six sigma concept in operations management using various examples and real-life case studies.
What is Six Sigma in Operations Management?
Six Sigma in operations management is a set of tools and techniques used in process improvement. Its primary purpose is to reduce variability and waste in processes and improve the output's quality. Six Sigma contains tools and techniques used to identify and quantify sources of variation and to find and implement solutions to eliminate them. The ultimate goal is to achieve near-perfect quality in all processes.
Six Sigma Principles for Operations Improvement
Master Right Skills & Boost Your Career
Avail your free 1:1 mentorship session
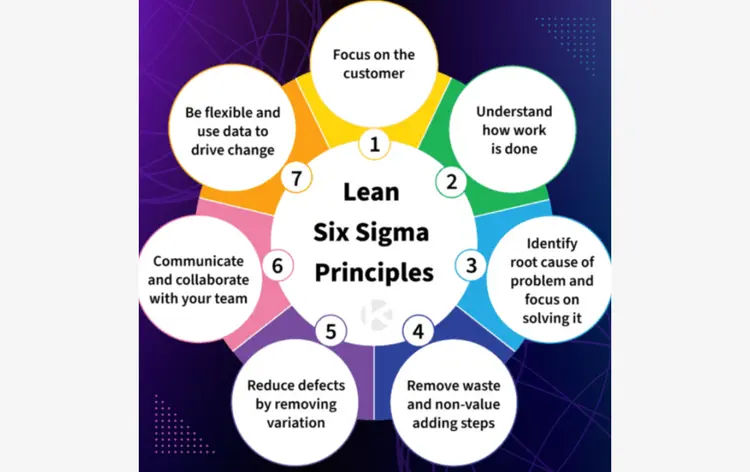
Six Sigma isn't a complex method to determine solutions. Instead, it has a clear objective – to provide authentic products and services for business development while ensuring optimum customer satisfaction. The basis of the Six sigma methodology lies in identifying the root cause of the problem and choosing the proper means to solve the problem. The following are the Six sigma principles for operations improvement:
1. Paying attention to the customer
There are many reasons why customer focus is important in Six Sigma for operations management. One reason is that it helps to ensure that the products and services being delivered meet the needs and wants of the customer. It is important because it can help improve customer satisfaction levels and reduce the number of complaints received. Additionally, customer focus can help improve the efficiency of operations by ensuring that the customers obtain the right products and services at the right time.
2. Ascertain the value stream and find the root cause of the problem
The value stream is the process that creates the product or service that the customer receives. To find and fix problems in the value stream, it is necessary first to measure them. Then, it helps to identify where the bottlenecks are and where improvements can be made.
There are several ways to measure the value stream, but one of the most important is to measure the cycle time. This is the time it takes to complete one cycle of the process, from start to finish. Measuring the cycle time can help to identify where the bottlenecks are and where improvements can be made.
Another critical metric is throughput. This is the number of units that can be processed in a given period. Measuring the throughput can help to identify where the bottlenecks are and where improvements can be made.
Finally, measuring the quality of the product or service is also important. This can be done in many ways, but one of the most important is to measure the defect rate. Measuring the defect rate can help to identify where the problems are and where improvements can be made.
3. Elimination of junk
Several steps are involved in eliminating defects in Six Sigma for operations management. The first step is to identify the root cause of the defects. This can be done through various methods, including process mapping, root cause analysis, and fishbone diagrams. Once the root cause of the defects has been identified, the next step is to develop a plan to correct the issue. This plan should be designed to prevent defects from occurring in the future. Finally, once the program is in place, it should be implemented and monitored to ensure that the defects are indeed being eliminated.
4. Comprehensive training of the operational hierarchy
Top-down training in Six Sigma is essential for operations management because it ensures that everyone in the organization is on the same page concerning the Six sigma methodology. It also ensures that everyone understands the importance of following the Six sigma methodology to achieve operational excellence.
5. Make sure you provide an interactive and sustainable workplace atmosphere
It is important to have a flexible and responsive workplace ecosystem in Six Sigma for operations management. First, it allows for quick and easy adaptation to changes in the market or environment. This is important because it can help an organization keep up with the competition and respond quickly to customer needs or demands changes.
Second, a flexible and responsive workplace ecosystem can help to improve employee morale and motivation. This is because employees feel more empowered when they can directly impact the organization and its success. Finally, a flexible and responsive workplace ecosystem can help improve an organization's overall efficiency. This is because it allows for better employee communication and collaboration and streamlined processes and procedures.
6. Create short-term projects with dedicated goals
The main purpose of developing short-term projects with specific goals in Six Sigma for operations management is to ensure that the organization's resources are used efficiently and effectively to achieve desired results. This includes providing that the right people are hired for the right jobs, that processes are designed and executed correctly, and that products and services meet customer expectations. Additionally, short-term projects with specific goals help to hold individuals and teams accountable for their performance and results.
Importance of Six Sigma in Operations Management
There are many ways that Six Sigma can impact operations, but some of the most common and significant ways are by reducing waste, improving quality, and increasing efficiency. By reducing waste, Six Sigma can help to improve the bottom line by ensuring that resources are used more effectively and efficiently. This can lead to high profits and a rise in shareholder value. To understand more about how Six Sigma helps with profitability, you can check out the Green Belt Certification online. It focuses on implementing Lean Six Sigma, its uses, and its performance in operations.
Additionally, by improving quality, Six Sigma can help to ensure that products and services meet or exceed customer expectations, leading to increased customer satisfaction and loyalty. Finally, by increasing efficiency, Six Sigma can help reduce operational costs and improve a company's overall competitiveness. The importance of Six Sigma in operations management can be noticed in the following aspects.
- Six Sigma is a data-driven approach to improving production and operations management.
- Six Sigma aims to reduce defects and variation in production and operations processes.
- Six Sigma uses statistical tools and methods to identify and track causes of defects and variation.
- Six Sigma seeks to eliminate waste and improve efficiency in production and operations processes.
- Six Sigma can help improve quality and customer satisfaction in production and operations processes.
- Six Sigma can help reduce costs associated with defects and variations in production and operations processes.
Six Sigma Approaches for Operations Management
The key approach of Six Sigma involves some critical steps, such as
- Define the problem and identify the goals.
- Measure the current performance.
- Analyze the causes of variation.
- Improve the process.
- Control the process to maintain the improvement.
- Sustain the improvement over time.
Six Sigma Tools for Operations Management
Moreover, there are a variety of tools that can be used in Six Sigma operations management, including:
- DMAIC: Define, Measure, Analyze, Improve, and Control. It is the standard Six Sigma methodology for improving existing processes.
- DFSS: Design for Six Sigma. It is a methodology used for designing new processes or products to achieve Six Sigma quality levels.
- Lean: A set of tools and principles for streamlining processes and reducing waste. Lean is often used in conjunction with Six Sigma.
- Six Sigma Calculators: There are a variety of online calculators that can be used to help with Six Sigma project planning and data analysis. Of all the tools used in Six Sigma operations management, the DMAIC remains the most efficient and demanding. DMAIC is an acronym for a Six Sigma tool made of phases like Define, Measure, Analyze, Improve, and Control. It is a problem-solving methodology used in Six Sigma to identify and correct defects in a process.
- The Define phase is all about learning about the problem. It includes identifying the goals, understanding the customer's needs, and defining the problem.
- The Measure phase is all about collecting data. The data is then analyzed to identify trends and patterns.
- The Analyze phase is all about understanding the root cause of the problem. Then, it helps to identify potential solutions.
- The Improve phase is all about implementing solutions. It includes designing and testing the solutions.
- The Control phase is all about maintaining the improvements. It includes monitoring the process and making changes as needed.
Simply put, Six Sigma tools use common sense to analyze and control a process of production or creation of service. For example, the Spaghetti Diagram is basically a diagram showing the manufacturing industry's working. It contains details about how things move around in creating a product as it passes down from one department to another. To analyze this diagram, you must look at the structure of the spaghetti. If the spaghetti is muddled up, the production chain faces hindrances, or there is a waste of time and money as the product moves around, causing delays. In this case, the concept of Six Sigma in production and operations management can help solve this situation by redesigning the floor plan or removing the obstacles.
Other Six sigma tools for operations management
- Cause and Effect Analysis
- Flow Chart
- Pareto Chart
- Histogram
- Check Sheet
- Scatter Plot
- Control Chart
Implementing Six Sigma Initiatives in Ops Management
There is no single answer to this question, as it can vary depending on the organization and the specific Six Sigma initiative being implemented. However, some general steps that are often involved in implementing a Six Sigma initiative in an organization's operations management include:
- Defining the problem or opportunity that the initiative will address.
- Drafting a plan for the initiative, including its goals, objectives, and timeline.
- Assigning responsibility for leading and carrying out the initiative to a Six Sigma team.
- Training the team members on the Six Sigma methodology and tools.
- Conducting a Six Sigma project to address the problem or opportunity.
- Evaluating the project results and making changes to the initiative as needed.
- institutionalizing the changes made through the initiative to ensure long-term success.
Unleash your career potential with PMP certification and placement, and land your dream job. Begin your project management journey now!
Real-life Use cases of Six Sigma in Ops Management
Operations Management is the process of ensuring that an organization's operations are efficient and effective. To achieve this, Operations Managers use various tools and techniques, one of which is Six Sigma.
There are many real-life examples of how Six Sigma has been used in Operations Management to achieve excellent results. For instance, GE Healthcare was able to reduce the manufacturing cycle time of one of its X-ray machines by 30% and reduce the number of defects by 90%. Another example is Motorola, which used Six Sigma to improve the quality of its cell phones and reduce the number of customer complaints by 60%.
These are two examples of Six Sigma in Operations Management to achieve great results. Implementing Six Sigma in your own organization can help you to improve quality, reduce costs, and increase customer satisfaction. Take a detailed look at how Six Sigma helped the companies mentioned above achieve various organizational goals.
- In 2002, Motorola implemented Six Sigma throughout its entire organization to improve customer satisfaction and reduce costs. As a result, the company achieved several successes, including reducing customer complaints and product defects and millions of dollars in cost savings.
- In 2003, GE launched a multi-year initiative to implement Six Sigma across all its businesses. The company achieved significant results, including a billion dollars worth of cost and defect reduction and a brilliant improvement in customer satisfaction.
- In 2004, Honeywell launched a Six Sigma initiative to reduce costs and improve customer satisfaction. As a result, the company achieved impressive results, including a reduction in product defects, improved customer satisfaction, and millions of dollars in cost savings.
Benefits of Six Sigma for Operations Management Professionals
There are many benefits that Six Sigma can bring to an organization, but here are benefits of Six Sigma in operations management that are especially relevant to operations management professionals:
- Six Sigma can help to improve efficiency and effectiveness in operations by identifying and eliminating waste and inefficiencies.
- The methodology enhances quality by identifying and eliminating sources of variation and defects.
- Six Sigma also reduces costs by identifying and eliminating waste and inefficiencies.
- Six Sigma can help to build on customer satisfaction by identifying and eliminating sources of variation and defects.
- Six Sigma can also work on employee satisfaction by providing them with a structured approach to problem-solving and continuous improvement.
- Under an ever-changing business scenario, Six Sigma can boost organizational competitiveness by providing a framework for continuous improvement.
Is Six Sigma Right for Your Company?
There is no one-size-fits-all answer to this question, as the appropriateness of Six Sigma will vary from company to company depending on factors such as the company's size, industry, and specific needs. However, some general tips that may help in determining if Six Sigma is suitable for a company to include:
- Assessing whether there is a genuine need for improvement in the company. Six Sigma is designed to help organizations improve their performance, so if there are no areas that require improvement, then Six Sigma may not be the best solution.
- Determining whether the company has the resources required to implement Six Sigma. Six Sigma can be a resource-intensive initiative, so companies must ensure they have the necessary personnel and financial resources before embarking on a Six Sigma project.
- Evaluating whether the company is ready for the change that Six Sigma will bring. Six Sigma can be a significant change for an organization, so it is vital to ensure that the company is prepared for the transition before moving forward with Six Sigma.
Conclusion
The Six Sigma methodology is a well-known and popular process improvement approach in many industries. Its popularity is due in part to its proven track record of success in improving process quality and efficiency. Students who wish to grasp the concept of Six Sigma in operations management can also opt for KnowledgeHut’s Six Sigma Certification course online. The Six Sigma approach can be adapted to many operations and business processes. When implemented correctly, it can significantly improve quality and productivity.
Frequently Asked Questions (FAQs)
1. Is a Six Sigma certification necessary?
2. How does Six sigma help in operation management?
3. Who should do Lean Six Sigma Green Belt certification?
Get Free Consultation
By submitting, I accept the T&C and
Privacy Policy