- Blog Categories
- Project Management
- Agile Management
- IT Service Management
- Cloud Computing
- Business Management
- Business Intelligence
- Quality Engineer
- Cyber Security
- Career
- Big Data
- Programming
- Most Popular Blogs
- PMP Exam Schedule for 2024: Check PMP Exam Date
- Top 60+ PMP Exam Questions and Answers for 2024
- PMP Cheat Sheet and PMP Formulas To Use in 2024
- What is PMP Process? A Complete List of 49 Processes of PMP
- Top 15+ Project Management Case Studies with Examples 2024
- Top Picks by Authors
- Top 170 Project Management Research Topics
- What is Effective Communication: Definition
- How to Create a Project Plan in Excel in 2024?
- PMP Certification Exam Eligibility in 2024 [A Complete Checklist]
- PMP Certification Fees - All Aspects of PMP Certification Fee
- Most Popular Blogs
- CSM vs PSM: Which Certification to Choose in 2024?
- How Much Does Scrum Master Certification Cost in 2024?
- CSPO vs PSPO Certification: What to Choose in 2024?
- 8 Best Scrum Master Certifications to Pursue in 2024
- Safe Agilist Exam: A Complete Study Guide 2024
- Top Picks by Authors
- SAFe vs Agile: Difference Between Scaled Agile and Agile
- Top 21 Scrum Best Practices for Efficient Agile Workflow
- 30 User Story Examples and Templates to Use in 2024
- State of Agile: Things You Need to Know
- Top 24 Career Benefits of a Certifed Scrum Master
- Most Popular Blogs
- ITIL Certification Cost in 2024 [Exam Fee & Other Expenses]
- Top 17 Required Skills for System Administrator in 2024
- How Effective Is Itil Certification for a Job Switch?
- IT Service Management (ITSM) Role and Responsibilities
- Top 25 Service Based Companies in India in 2024
- Top Picks by Authors
- What is Escalation Matrix & How Does It Work? [Types, Process]
- ITIL Service Operation: Phases, Functions, Best Practices
- 10 Best Facility Management Software in 2024
- What is Service Request Management in ITIL? Example, Steps, Tips
- An Introduction To ITIL® Exam
- Most Popular Blogs
- A Complete AWS Cheat Sheet: Important Topics Covered
- Top AWS Solution Architect Projects in 2024
- 15 Best Azure Certifications 2024: Which one to Choose?
- Top 22 Cloud Computing Project Ideas in 2024 [Source Code]
- How to Become an Azure Data Engineer? 2024 Roadmap
- Top Picks by Authors
- Top 40 IoT Project Ideas and Topics in 2024 [Source Code]
- The Future of AWS: Top Trends & Predictions in 2024
- AWS Solutions Architect vs AWS Developer [Key Differences]
- Top 20 Azure Data Engineering Projects in 2024 [Source Code]
- 25 Best Cloud Computing Tools in 2024
- Most Popular Blogs
- Company Analysis Report: Examples, Templates, Components
- 400 Trending Business Management Research Topics
- Business Analysis Body of Knowledge (BABOK): Guide
- ECBA Certification: Is it Worth it?
- How to Become Business Analyst in 2024? Step-by-Step
- Top Picks by Authors
- Top 20 Business Analytics Project in 2024 [With Source Code]
- ECBA Certification Cost Across Countries
- Top 9 Free Business Requirements Document (BRD) Templates
- Business Analyst Job Description in 2024 [Key Responsibility]
- Business Analysis Framework: Elements, Process, Techniques
- Most Popular Blogs
- Best Career options after BA [2024]
- Top Career Options after BCom to Know in 2024
- Top 10 Power Bi Books of 2024 [Beginners to Experienced]
- Power BI Skills in Demand: How to Stand Out in the Job Market
- Top 15 Power BI Project Ideas
- Top Picks by Authors
- 10 Limitations of Power BI: You Must Know in 2024
- Top 45 Career Options After BBA in 2024 [With Salary]
- Top Power BI Dashboard Templates of 2024
- What is Power BI Used For - Practical Applications Of Power BI
- SSRS Vs Power BI - What are the Key Differences?
- Most Popular Blogs
- Data Collection Plan For Six Sigma: How to Create One?
- Quality Engineer Resume for 2024 [Examples + Tips]
- 20 Best Quality Management Certifications That Pay Well in 2024
- Six Sigma in Operations Management [A Brief Introduction]
- Top Picks by Authors
- Six Sigma Green Belt vs PMP: What's the Difference
- Quality Management: Definition, Importance, Components
- Adding Green Belt Certifications to Your Resume
- Six Sigma Green Belt in Healthcare: Concepts, Benefits and Examples
- Most Popular Blogs
- Latest CISSP Exam Dumps of 2024 [Free CISSP Dumps]
- CISSP vs Security+ Certifications: Which is Best in 2024?
- Best CISSP Study Guides for 2024 + CISSP Study Plan
- How to Become an Ethical Hacker in 2024?
- Top Picks by Authors
- CISSP vs Master's Degree: Which One to Choose in 2024?
- CISSP Endorsement Process: Requirements & Example
- OSCP vs CISSP | Top Cybersecurity Certifications
- How to Pass the CISSP Exam on Your 1st Attempt in 2024?
- Most Popular Blogs
- Best Career options after BA [2024]
- Top Picks by Authors
- Top Career Options & Courses After 12th Commerce in 2024
- Recommended Blogs
- 30 Best Answers for Your 'Reason for Job Change' in 2024
- Recommended Blogs
- Time Management Skills: How it Affects your Career
- Most Popular Blogs
- Top 28 Big Data Companies to Know in 2024
- Top Picks by Authors
- Top Big Data Tools You Need to Know in 2024
- Most Popular Blogs
- Web Development Using PHP And MySQL
- Top Picks by Authors
- Top 30 Software Engineering Projects in 2024 [Source Code]
- More
- Tutorials
- Practise Tests
- Interview Questions
- Free Courses
- Agile & PMP Practice Tests
- Agile Testing
- Agile Scrum Practice Exam
- CAPM Practice Test
- PRINCE2 Foundation Exam
- PMP Practice Exam
- Cloud Related Practice Test
- Azure Infrastructure Solutions
- AWS Solutions Architect
- AWS Developer Associate
- IT Related Pratice Test
- ITIL Practice Test
- Devops Practice Test
- TOGAF® Practice Test
- Other Practice Test
- Oracle Primavera P6 V8
- MS Project Practice Test
- Project Management & Agile
- Project Management Interview Questions
- Release Train Engineer Interview Questions
- Agile Coach Interview Questions
- Scrum Interview Questions
- IT Project Manager Interview Questions
- Cloud & Data
- Azure Databricks Interview Questions
- AWS architect Interview Questions
- Cloud Computing Interview Questions
- AWS Interview Questions
- Kubernetes Interview Questions
- Web Development
- CSS3 Free Course with Certificates
- Basics of Spring Core and MVC
- Javascript Free Course with Certificate
- React Free Course with Certificate
- Node JS Free Certification Course
- Data Science
- Python Machine Learning Course
- Python for Data Science Free Course
- NLP Free Course with Certificate
- Data Analysis Using SQL
8 Wastes in Lean Six Sigma
Updated on Nov 05, 2022 | 15 min read | 10.3k views
Share:
Waste is the dead weight that does nothing but brings the project value down. It can be wasted time, resources, or efforts that never yield any results. Any waste in lean Six Sigma will result in lowering productivity levels and might as well lead to project failures. That is why every organization plans to reduce its overall wastage and increase project value too many folds. They appoint qualified professionals to study current company operations and create plans to eliminate or at least effectively reduce waste.
They hire somebody preferably with the lean Six Sigma certification, as they will be proficient with a comprehensive understanding of the techniques and strategies that can help reduce waste efficiently enough to improve overall company operations. If you are an organization looking for ways to eliminate waste, hiring qualified professionals with a comprehensive understanding of the 8 wastes downtime is crucial. On the other hand, if you are a candidate, taking up a certification course can be your first step toward a successful and promising career. Let us discuss the 8 wastes of lean Six Sigma for better clarity.
What are 8 Wastes in Lean Six Sigma
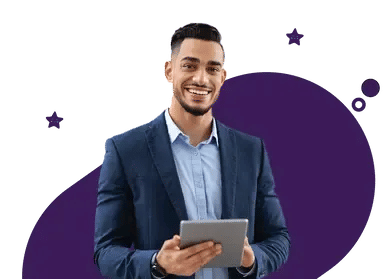
Master Right Skills & Boost Your Career
Avail your free 1:1 mentorship session
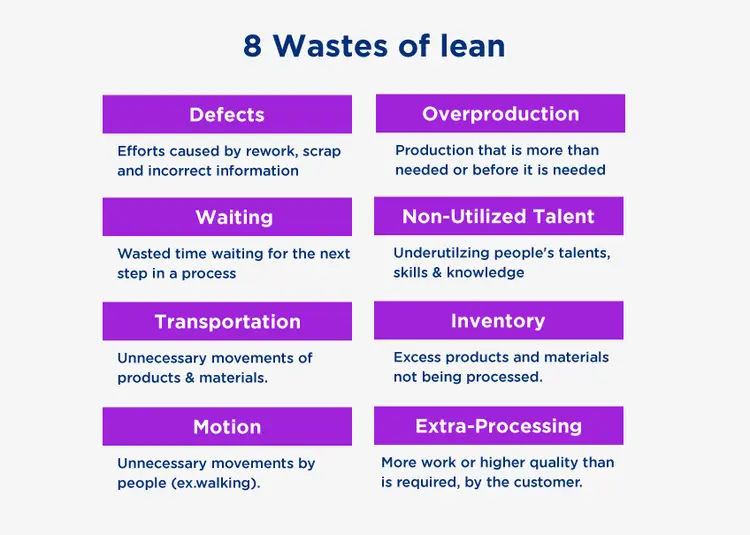
In lean manufacturing, you will find challenges depicted as wastes that reduce the chances of project success. Time and resources are the fundamental downtime lean waste, as it accounts for the significant loss in productivity levels. Additionally, if there are defects in a project, the team would have to spend more time, effort, and resources on it to resolve the issue before delivery. All of this together fall into the category of 6 sigma waste. The concern of every organization is to eliminate that waste to increase overall productivity.
Let’s see the 8 wastes in six sigma:
- Over Production
- Defects
- Waiting
- Transportation
- Unused Talent
- Inventory
- Motion
- Extra Processing
To start working on something, one has to understand the task well. Hence, to eliminate waste during a project, one has to know about the types of waste Six Sigma. Let us check these in details.
1. Over Production
Some organizations produce things even before their requirement pops up, wasting time and resources in manufacturing. Furthermore, some teams overestimate the requirements and manufacture unnecessarily large units of products. As a result, the demand doesn't meet the manufacturer's expectations, leading to overproduction. The goods produced are useless, so the resources and efforts they put into manufacturing also go waste. Some of the common reasons behind overproduction are:
- Zero strategies in manufacturing units
- Inaccurate forecast and demand expectations
- Unclear consumer requirements
- Not keeping track of production routines
These are the common causes of overproduction that makes up for a significant waste in a project.
2. Defects
Not paying enough attention to the flaws during the production process leads to multiple defects that only result in a flawed end product. No client or consumer would accept defective products, so it is clear that you have wasted all your time, effort, resources, and capital. Some of the common reasons behind defects are:
- Poor quality control
- Lack of clarity during requirement gathering
- Improper functioning of the machinery or tools involved
These and multiple other factors lead to increased defects in the end product, a significant type of waste.
3. Waiting
Waiting for resources or putting human efforts on hold is all about the waiting waste. You may not consider, but all this wait costs the company additional expenses, and it will reduce the project value significantly. In simple words, waiting is the opposite of overproduction, where the organization puts the project on hold and doesn’t have enough to offer to its clients. The reasons behind waiting are:
- Poor communication among teams
- Idle equipment which nobody needs
- Delayed setups or lack of control over the processes
Apart from this, the factor leading to waiting includes unplanned downtime.
4. Transportation
The operations happen at varied locations in the industries spread across a large area. Thus, there will be a lot of transportation of goods, accessories, and humans to complete a project. If the site gets designed by experts, at least units that have to work collaboratively stand nearby to reduce transportation expenses and time. However, if the design is poor, you would have to consider transportation as waste. The primary reason behind this waste is poor site design or lack of strategy while managing the unit.
5. Unused Talent
It is one of the most significant losses associated with not using the available talent efficiently. The management team doesn’t pay attention to how they can allot tasks to people considering who would do what to the best of their capability. For example, if you have an employee with a financial background, assigning inventory management tasks to them is a blunder! Thus, it is essential to divide the task smartly, ensuring no talent goes unnoticed and everyone contributes towards the project to the best of their abilities.
6. Inventory
Holding the raw materials and resources used for product manufacturing results in inventory waste. You will have to allocate space to things that are not required in the near future and will have to bear the storage expenses. Additionally, everything will go to waste if the product isn't used soon! All of it happens due to mismanagement and not keeping track of the production processes, and this wastage of resources, capital, and time leads to lower productivity levels.
7. Motion
To move people and things from one place to another will cost money. So, if your manufacturing site is far from the storage unit, consider the additional charges as waste. The more you want to move these things your total expense on the project will also increase. Another waste category in Six Sigma is the significant amount of time that goes into this process.
8. Extra Processing
To keep processing information unnecessarily is the eighth waste type in Six Sigma. It often happens when the communication between the teams is not efficient. However, it can also occur due to human error or delayed approvals by management. Whatever the reason is, extra processing is a waste that drastically impacts project success.
These are eight types of wastes that lead to downtime Six Sigma. It can affect productivity levels, increase project costs, and even lead to failure. Let us discuss a few lean waste examples for better clarity.
How to Endure Negligible Downtime
The most significant waste factor includes downtime in Six Sigma and lean waste. It might happen due to candidates sitting idle and not giving their best or one team waiting for the other to complete a connecting task and sitting idle till then. Companies try to find solutions to eliminate waste by replacing the dead weight with something more fruitful. Furthermore, they bring the necessary tools and techniques into the picture to improve the project’s potential by eliminating the waste factors. Simple things they do to ensure negligible downtime are:
- Ensuring that the company operations happen smoothly and seamlessly so that the teams working together do not have to waste time waiting.
- Giving relevant tasks to people, keeping their abilities or talents in mind to ensure no resource gets wasted when the project is in process.
- Eliminating the downtime that happens due to a shortage of resources or other factors. For example, people might have to wait till management starts the meeting or till the higher authorities provide them with the required resources.
- Organize the inventory and the administrative task, leaving no stone unturned in achieving zero downtime and maximum productivity levels.
There are multiple other strategies or proven techniques that every organization uses for Six sigma waste reduction. The question that might arise here is, what exactly happens if you do not remove waste or why is it necessary to remove them from your project? Let us dig deeper and discuss this in detail.
Why it is Important to Remove Six Sigma Wastes
Waste identification and elimination from a project are essential as they might lead to complete failure or lower the overall value significantly. Moreover, even if you complete the project successfully, the profitability will not be as fruitful as it can be if you do not pay attention to waste elimination.
It is not easy to remove every possibility of waste, but hiring qualified experts with Green Belt courses can prove fruitful. These experts can identify the issues or the waste types that reduce your project value. They analyze the current situation, identify triggers, and curate strategic plans to ensure project success. If your choice of experts is apt, you can rest assured that Six sigma waste elimination will never be an issue!
The most significant waste factor includes downtime in Six Sigma and lean waste. It might happen due to candidates sitting idle and not giving their best or one team waiting for the other to complete a connecting task and sitting idle till then. Companies try to find solutions to eliminate waste by replacing the dead weight with something more fruitful. Furthermore, they bring the necessary tools and techniques into the picture to improve the project’s potential by eliminating the waste factors. Simple things they do to ensure negligible downtime are:
- Ensuring that the company operations happen smoothly and seamlessly so that the teams working together do not have to waste time waiting.
- Giving relevant tasks to people, keeping their abilities or talents in mind to ensure no resource gets wasted when the project is in process.
- Eliminating the downtime that happens due to a shortage of resources or other factors. For example, people might have to wait till management starts the meeting or till the higher authorities provide them with the required resources.
- Organize the inventory and the administrative task, leaving no stone unturned in achieving zero downtime and maximum productivity levels.
There are multiple other strategies or proven techniques that every organization uses for Six sigma waste reduction. The question that might arise here is, what exactly happens if you do not remove waste or why is it necessary to remove them from your project? Let us dig deeper and discuss this in detail.
Boost your project management exam success with our project management courses. Achieve certification and elevate your career!
8 Six Sigma Wastes Examples:
There are countless examples for each of the 8 types Six Sigma waste. We have categorized the real-life examples accordingly to help you understand them better.
1. Defects
Common defects you might face are misleading information on the charts or reports shared across the project team. Another example can be wrong labels on the containers or basically any other mistake that can lead to flawed actions.
2. Overproduction
Real-life examples of overproduction include printing unnecessary documents when you have the option to keep information on the computer system. Another option is to store the same information on multiple forms instead of segregating it into one.
3. Waiting
As the name suggests, waiting is when the client has to wait for the service delivery or if one team waits as the other sends information to start their work. Moreover, waiting is also when the team sits idle, waiting for the resources that the company has to provide.
4. Transportation
You can link it with moving assets unnecessarily from one place to another. It is also related to the event when one has to make too many mouse clicks on the website before getting the required information.
5. Inventory
Overstocking products even when you can do with much lesser quantity. Keeping unnecessary documents and files in the office cabinets is also an example of waste.
6. Unused Talent
Not assigning tasks as per talents is significant waste in an organization. Moreover, not organizing staff training to update the skills also leads to asset wastage.
7. Motion
Excessive staff movement to fetch things they require is a waste associated with time.
8. Extra Processing
Processing the same information over again is a waste of time, effort, and resources. Once you get satisfactory test results, move ahead and do not keep processing them.
These real-life scenarios would have given you an elaborate idea of what ‘waste’ refers to in any project. So, if you are a project manager or simply a person concerned with project efficiency, identify if you see any such waste around you and take necessary actions to eliminate its impact.
Conclusion
Lean Six sigma waste types can turn the tables around and result in project failures. The first step to eliminate these risk factors is identifying them and finding replacements that can reduce downtime. Organizations can hire experts who have done some specific certification in the domain and hand over the task to them. They will identify the trigger, see where the company operations are lacking and create strategies to improve the project productivity. They work dedicatedly toward these things, and the results are always outstanding.
If you are a student or professional, know that it is a fruitful domain with the best salary packages to offer. So, you should take the KnowledgeHut lean Six Sigma certification and grab better opportunities in the job market. Once you gain proficiency, there is no looking back! Your professional journey gets better, and your future is secured.
Frequently Asked Questions (FAQs)
1. What are the 8 types of waste?
2. What is the 8th waste?
3. What are the 8 wastes of Lean management?
4. What are the eight general wastes in manufacturing?
Get Free Consultation
By submitting, I accept the T&C and
Privacy Policy