- Blog Categories
- Project Management
- Agile Management
- IT Service Management
- Cloud Computing
- Business Management
- Business Intelligence
- Quality Engineer
- Cyber Security
- Career
- Big Data
- Programming
- Most Popular Blogs
- PMP Exam Schedule for 2024: Check PMP Exam Date
- Top 60+ PMP Exam Questions and Answers for 2024
- PMP Cheat Sheet and PMP Formulas To Use in 2024
- What is PMP Process? A Complete List of 49 Processes of PMP
- Top 15+ Project Management Case Studies with Examples 2024
- Top Picks by Authors
- Top 170 Project Management Research Topics
- What is Effective Communication: Definition
- How to Create a Project Plan in Excel in 2024?
- PMP Certification Exam Eligibility in 2024 [A Complete Checklist]
- PMP Certification Fees - All Aspects of PMP Certification Fee
- Most Popular Blogs
- CSM vs PSM: Which Certification to Choose in 2024?
- How Much Does Scrum Master Certification Cost in 2024?
- CSPO vs PSPO Certification: What to Choose in 2024?
- 8 Best Scrum Master Certifications to Pursue in 2024
- Safe Agilist Exam: A Complete Study Guide 2024
- Top Picks by Authors
- SAFe vs Agile: Difference Between Scaled Agile and Agile
- Top 21 Scrum Best Practices for Efficient Agile Workflow
- 30 User Story Examples and Templates to Use in 2024
- State of Agile: Things You Need to Know
- Top 24 Career Benefits of a Certifed Scrum Master
- Most Popular Blogs
- ITIL Certification Cost in 2024 [Exam Fee & Other Expenses]
- Top 17 Required Skills for System Administrator in 2024
- How Effective Is Itil Certification for a Job Switch?
- IT Service Management (ITSM) Role and Responsibilities
- Top 25 Service Based Companies in India in 2024
- Top Picks by Authors
- What is Escalation Matrix & How Does It Work? [Types, Process]
- ITIL Service Operation: Phases, Functions, Best Practices
- 10 Best Facility Management Software in 2024
- What is Service Request Management in ITIL? Example, Steps, Tips
- An Introduction To ITIL® Exam
- Most Popular Blogs
- A Complete AWS Cheat Sheet: Important Topics Covered
- Top AWS Solution Architect Projects in 2024
- 15 Best Azure Certifications 2024: Which one to Choose?
- Top 22 Cloud Computing Project Ideas in 2024 [Source Code]
- How to Become an Azure Data Engineer? 2024 Roadmap
- Top Picks by Authors
- Top 40 IoT Project Ideas and Topics in 2024 [Source Code]
- The Future of AWS: Top Trends & Predictions in 2024
- AWS Solutions Architect vs AWS Developer [Key Differences]
- Top 20 Azure Data Engineering Projects in 2024 [Source Code]
- 25 Best Cloud Computing Tools in 2024
- Most Popular Blogs
- Company Analysis Report: Examples, Templates, Components
- 400 Trending Business Management Research Topics
- Business Analysis Body of Knowledge (BABOK): Guide
- ECBA Certification: Is it Worth it?
- How to Become Business Analyst in 2024? Step-by-Step
- Top Picks by Authors
- Top 20 Business Analytics Project in 2024 [With Source Code]
- ECBA Certification Cost Across Countries
- Top 9 Free Business Requirements Document (BRD) Templates
- Business Analyst Job Description in 2024 [Key Responsibility]
- Business Analysis Framework: Elements, Process, Techniques
- Most Popular Blogs
- Best Career options after BA [2024]
- Top Career Options after BCom to Know in 2024
- Top 10 Power Bi Books of 2024 [Beginners to Experienced]
- Power BI Skills in Demand: How to Stand Out in the Job Market
- Top 15 Power BI Project Ideas
- Top Picks by Authors
- 10 Limitations of Power BI: You Must Know in 2024
- Top 45 Career Options After BBA in 2024 [With Salary]
- Top Power BI Dashboard Templates of 2024
- What is Power BI Used For - Practical Applications Of Power BI
- SSRS Vs Power BI - What are the Key Differences?
- Most Popular Blogs
- Data Collection Plan For Six Sigma: How to Create One?
- Quality Engineer Resume for 2024 [Examples + Tips]
- 20 Best Quality Management Certifications That Pay Well in 2024
- Six Sigma in Operations Management [A Brief Introduction]
- Top Picks by Authors
- Six Sigma Green Belt vs PMP: What's the Difference
- Quality Management: Definition, Importance, Components
- Adding Green Belt Certifications to Your Resume
- Six Sigma Green Belt in Healthcare: Concepts, Benefits and Examples
- Most Popular Blogs
- Latest CISSP Exam Dumps of 2024 [Free CISSP Dumps]
- CISSP vs Security+ Certifications: Which is Best in 2024?
- Best CISSP Study Guides for 2024 + CISSP Study Plan
- How to Become an Ethical Hacker in 2024?
- Top Picks by Authors
- CISSP vs Master's Degree: Which One to Choose in 2024?
- CISSP Endorsement Process: Requirements & Example
- OSCP vs CISSP | Top Cybersecurity Certifications
- How to Pass the CISSP Exam on Your 1st Attempt in 2024?
- Most Popular Blogs
- Best Career options after BA [2024]
- Top Picks by Authors
- Top Career Options & Courses After 12th Commerce in 2024
- Recommended Blogs
- 30 Best Answers for Your 'Reason for Job Change' in 2024
- Recommended Blogs
- Time Management Skills: How it Affects your Career
- Most Popular Blogs
- Top 28 Big Data Companies to Know in 2024
- Top Picks by Authors
- Top Big Data Tools You Need to Know in 2024
- Most Popular Blogs
- Web Development Using PHP And MySQL
- Top Picks by Authors
- Top 30 Software Engineering Projects in 2024 [Source Code]
- More
- Tutorials
- Practise Tests
- Interview Questions
- Free Courses
- Agile & PMP Practice Tests
- Agile Testing
- Agile Scrum Practice Exam
- CAPM Practice Test
- PRINCE2 Foundation Exam
- PMP Practice Exam
- Cloud Related Practice Test
- Azure Infrastructure Solutions
- AWS Solutions Architect
- AWS Developer Associate
- IT Related Pratice Test
- ITIL Practice Test
- Devops Practice Test
- TOGAF® Practice Test
- Other Practice Test
- Oracle Primavera P6 V8
- MS Project Practice Test
- Project Management & Agile
- Project Management Interview Questions
- Release Train Engineer Interview Questions
- Agile Coach Interview Questions
- Scrum Interview Questions
- IT Project Manager Interview Questions
- Cloud & Data
- Azure Databricks Interview Questions
- AWS architect Interview Questions
- Cloud Computing Interview Questions
- AWS Interview Questions
- Kubernetes Interview Questions
- Web Development
- CSS3 Free Course with Certificates
- Basics of Spring Core and MVC
- Javascript Free Course with Certificate
- React Free Course with Certificate
- Node JS Free Certification Course
- Data Science
- Python Machine Learning Course
- Python for Data Science Free Course
- NLP Free Course with Certificate
- Data Analysis Using SQL
An Overview of Kanban System Examples
Updated on Aug 25, 2022 | 12 min read | 10.5k views
Share:
Table of Contents
In the early 1940s, Toyota automotive in Japan used a simple planning system to manage and control work and inventory at each stage optimally. Kanban also spelled “kamban” in the Japanese language, means available work capacity. It is related to lean and just-in-time JIT production, where it is used as a scheduling system to indicate what to produce, when, and how much.
Kanban is a visual system of work management that visualizes both the process or workflow and the actual work going through that process. The goal is to figure out the potential bottlenecks in the process and fix them so that the work continues at optimal speed and cost-effectively. The growing popularity of Kanban since then has popularized Kanban training.
The beauty of Kanban is, it can even be used at a personal level to enhance your personal productivity by managing work and personal responsibilities efficiently. The idea of using Kanban at a personal level was first introduced by Jim Benson and Tonianne DeMaria Barry in the book “Personal Kanban: Mapping Work | Navigating Life”. Here they talk about a system for prioritizing tasks and improving overall productivity.
How does Kanban System work?
Kanban is a way to gradually improve whatever you do, be it software development, IT or operations, recruitment, procurement, marketing, sales, or other things. Any business can benefit from the lean Kanban methodology.
As per a research, handling work pressure and family responsibilities cause stress in 80% of people. By modifying some Kanban rules you can not only save time and improve efficiency but can also reduce the feeling of being stressed.
A Kanban method example for managing your long personal To-Do list could be using a personal Kanban board (physical whiteboard or Kanban project management software ). You can create columns like: To Do -> In Progress -> Complete.
Here is a simple personal Kanban board example that can be used at the workplace to manage your own tasks:
Insider Tips to Land Your Dream Scrum Master Job
Includes Scrum Resume Sample
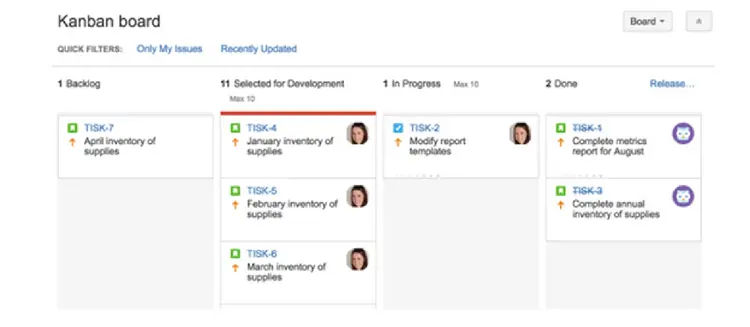
If you choose Kanban project management software, here is a Kanban board example Jira.
Kanban uses principles and non-disruptive practices for managing and improving work flow and promotes gradual improvements to an organizational process. Kanban uses 4 foundational principles. These Kanban rules are:
1. Whatever you are Doing Right Now, Start from There
Do not try to make any changes to the existing process right away. Any required changes should be applied gradually over a period of time and at a pace the team members are comfortable with.
2. Make a Commitment to Pursue Incremental Changes
Instead of trying to make radical and drastic changes that might create resistance among the members, bring small progressive changes bit by bit.
3. Respect the Present Roles, Responsibilities, and Job Titles
Kanban does not impose organizational changes in existing roles and functions that might perform well. Instead, let the team collaboratively identify and implement any required alterations. The fear of change and emotional resistance will not happen if worked this way.
4. Encourage Leadership at all Levels
Since Kanban encourages gradual and continuous improvements at all levels of an organization, it does not believe that leadership has to originate from the senior hierarchy alone. Workers at all levels can show ideas and acts of leadership to implement changes and continue to improve their products or services.
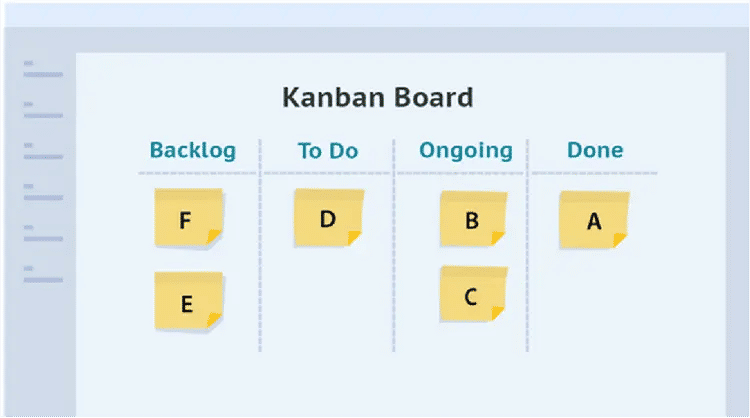
Kanban Uses 6 Core Practices
The core practices of Kanban are:
1. Visualization
The entire workflow must be visualized using a physical or an electronic Kanban Board. The Kanban board can be very simple to elaborate on, depending on the work. Once this is done, the team members' current task can be visualized using stickies/cards with different colors.
2. Limiting the Work in Progress (WIP)
By limiting WIP the team can first complete the task at hand and marked ‘done’ before taking up a new one. This creates the capacity in the system to ‘pull in’ new work.
Kanban uses the ‘pull system’ method to reduce production waste, that is, producing what is required after the previous batch has been consumed. A very simple Kanban pull system example is your local fast-food shop. Here production only happens when a customer places the order. Ideally, you can start with no WIP limits to understand and define WIP limits for each stage of the workflow once you have sufficient data. The usual practice is to start with a WIP limit of 1 to 1.5 times the members working in a specific stage.
Another advantage of setting WIP is it communicates to the clients or stakeholders the capacity limit of working for a team so that they can plan the work expectation accordingly.
3. Manage Workflow
There will either be a smooth flow within WIP limits or a piling up of work depending on how well the workflow is defined and WIP limits are set. The key aspect of this phase is understanding and analyzing the system and making the needed adjustments to improve workflow and reduce the time consumed to complete the work. Because the bottlenecks to be adjusted get visible. As a result, workflow improves, work completion becomes more predictable, and it helps to make reliable commitments to clients and stakeholders.
Here is one of the Kanban inventory system examples using Kanban board:
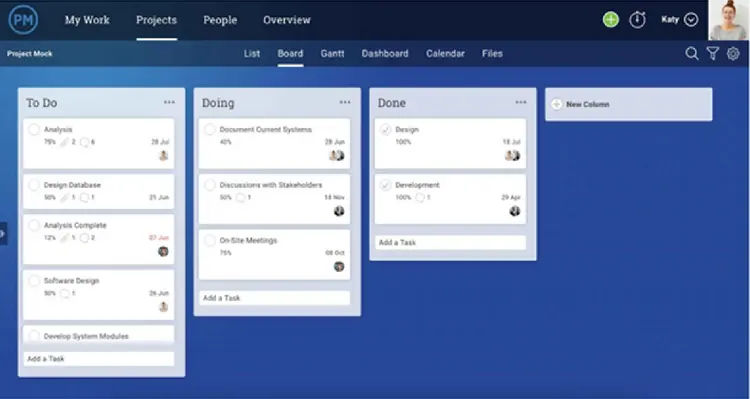
4. Make Policies Transparent and Stated
Defining and visualizing the rules or guidelines helps all involved to understand ‘how to work.’ An example of explicit policy could be, defining clearly when a task will be considered complete.
5. Implement Various Feedback Loops
Various types of feedback loops must be implemented. Keep reviewing stages in the Kanban workflow, metrics, reports, and other visual cues that provide constant feedback on the work in progress. Getting feedback early on helps to keep the work on track and timely delivery of quality output.
6. Improve and Evolve
Kanban is a gradual or evolutionary process of improving by adopting small changes. At a manageable pace. Kanban urges the use of scientific ways of evolution.
First, you deduce a hypothesis, test it and make the needed changes depending on the result obtained. By implementing Lean or Agile principles, the focus is to evaluate the processes continuously and improve constantly. The impact of each change introduced should be observed and measured using various systems of Kanban that signal if you are improving or not. Accordingly, you can keep the changes or try something new. Using the SwiftKanban free tool, for example, you can evaluate your performance.
Attending a Kanban training course introduces Kanban, and shows how using Kanban as a tool can build better quality products with real-world case study examples.
Kanban System in Lean Manufacturing (With Examples)
Kanban itself is a part of the “lean production” or “lean manufacturing” system that uses techniques to remove wastage of any kind be it labor or inventory. It implements production through a ‘pull-system’ instead of responding to predicted demand. A drastic shift from the traditional way of production as per anticipated or forecasted demand, making materials available in bulk to reduce supply chain costs like transport.
Kanban cuts waste and improves communication on client orders keeping all on the same platform of understanding of the happenings / current status all the time.
Some examples of companies using Kanban in lean manufacturing are mentioned below:
Jaguar
The company faced the issue of delayed feedback on design concepts and designs. Sometimes it took twelve or more weeks.
By using the Kanban way of ‘minimum viable product concept’ of giving the stakeholders just the information they need to make a decision ( cutting off the irrelevant details). Additionally, decreasing batch sizes it reduced the feedback cycle from weeks to days. Kanban proved to be a massive success for Jaguar.
The company has now become a leader in lean manufacturing by reducing delivery time and improving quality.
Pixar Animation Studios
The company implemented Kanban board and lean manufacturing principles to its 3D animation to ensure that each Pixar production was manufactured.
Through a high-level Kanban board, the team members could see what the other teams are working on. Besides, each team ensured its role in the film production was complete before passing it on to the next team.
In turn, it also meant anyone could stop the production line if any error occurred. It ensured that the faulty thing did not pass onto the next team down the line just to grow more expensive to mend.
Enroll in our comprehensive PMP certification preparation course and maximize your potential as a project manager. Enhance your skills and soar to new heights in your career!
Kanban System Examples
Kanban is way beyond a process visualization on a white or electronic board and working with stickies or electronic cards. Organizations from large to start-ups reap huge benefits from the methodical implementation of its principles and practices. IT companies including Microsoft received the benefits of Kanban, though Kanban is not a software development tool or a project management methodology framework. Essentially, the beauty of Kanban lies in its simplicity and it is a way of continuously improving one’s work progress.
The software development operations of Microsoft used Kanban way back in 2004. Since then, it has been adopted by the DevOps, application, and software teams. Here lies another appeal of Kanban. It can be applied to any process or methodologies like Scrum, XP, or any other traditional methods like an iterative, waterfall, or anything else. Kanban just needs to be started just where you stand and take small steps towards improvement continuously.
In the IT sector, Kanban has undergone its own evolution. It now works to bring agility in managing and improving service delivery in a measured, unhurried and continuous way. It helps better manage SLAs (Service Level Agreements) for timely delivering products minimizing risks and costs of delay.
Likewise, application software and tech product teams have benefitted from the Kanban way of lean and agile principles. The teams get fabulous visualization of their work, delivering quality products and services continuously on time and receiving customer feedback more often and at a greater speed.
Discover the leading Agile Category Courses
Types of Kanban System
Here are some major Kanban types:
Production Kanban
The basic type of Kanban and mostly used. It starts with an exhaustive list of all tasks required to be completed within a stipulated time. The production Kanban asks the production to start after explaining the quality and quantity required.
Withdrawal / Conveyance Kanban
Basically, it involves the movement of products (physical or digital). Any work needs the involvement of different teams contributing to it. When a team has finished its part, it is moved to the next team. The teams use withdrawal / movement cards to alert members that one task is over and is ready to move on to the next section so that the next team is ready to take it. At the same time, the current team signals to the previous team that it is now ready for fresh work.
Supplier Kanban
This is a special type of Kanban that businesses use to include suppliers within their Kanban system of work. Here supplier cards are sent to the supplier indicating a new batch of a specific item to be delivered.
Instead of depending on the procurement department to get in touch with suppliers and again waiting for feedback from the procurement department, a concerned team can communicate with the supplier directly and get the work done. Working this way ensures timely delivery of material without unnecessary waiting periods, delays, and follow-ups.
Emergency Kanban
To meet unexpected situations requiring immediate attention Emergency Kanban is used. Emergency cards signal the replacement need of a faulty part or any sudden change needed in the quality of a product. These also help to raise a signal to the team working previously on the job to ensure that the rest of the items in the lot do not have the same issue.
If the problem is serious, emergency cards can be sent to all the teams involved to stop the work while the team dealing with the problem gets the issue sorted.
The idea is not to generate waste by using faulty material or waste time in asking for an item that has been found defective and needs to be replaced. Everyone in the chain is kept informed of the happening and thus smooth functioning can happen.
Express Kanban
Quite similar to Emergency Kanban, Express Kanban also deals with emergency situations that demand immediate resolution. The difference is, that Express Kanban deals with shortages (instead of defects) of a specific item.
Emergency signal cards are sent in case of short or very low supply and might even ask the production process to slow down or stop altogether till the supply is resumed. The idea is to avoid the smooth functioning of production.
Conclusion
To conclude, the reach of Kanban is much beyond just manufacturing, production or IT environments. With great agility, it fits into any environment, tech or non-tech bringing huge blessings to organizations and teams who want to produce high-quality products or services. Even creative companies and agencies believe in Kanban and use it to streamline processes, eliminate waste and improve quality. KnowledgeHut Kanban training can be explored in this respect. The learners come out armed with a full understanding of the intent and practices of Kanban and the skill of using it.
Frequently Asked Questions (FAQs)
1. What is the use of Kanban in day-to-day life?
2. What are the 6 core practices of Kanban?
3. What are the types of Kanban Systems?
Get Free Consultation
By submitting, I accept the T&C and
Privacy Policy
Ready to lead with Scrum expertise?